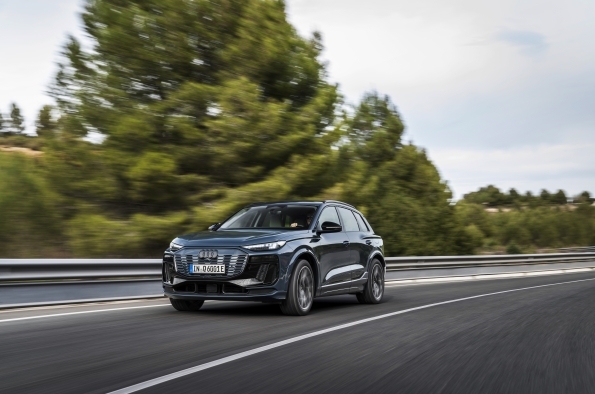
A technological leap for the next generation of fully electric mobility from Audi
London, 17 May 2024, (Oilandgaspress) –The Premium Platform Electric (PPE), developed jointly with Porsche, is a key component for the expansion of the global portfolio of all-electric Audi models. For Audi, it represents an important step in becoming a leading provider of sustainable premium mobility. For the next generation of electric vehicles from Audi, the company has redeveloped the electric motors, the power electronics, the transmission, as well as the high-voltage battery and all related components, and tailored them exactly to the requirements of battery electric vehicles.
What differentiates the electric motor for the PPE from the electric drive systems that have been used to date?
All powertrain components for the PPE are designed to be even more compact than the drive systems developed and installed previously, and they stand out due to higher efficiency. In the area of production, the degree of automation and the vertical range of manufacture have increased significantly. The new electric motors for the PPE require about 30 percent less installation space than those of previous electric models. Their weight has been reduced by about 20 percent.
The PSM (permanent magnet synchronous motor) on the rear axle of the Audi Q6 e-tron series has a length of 200 millimeters. The ASM (asynchronous motor) on the front axle has a length of 100 millimeters. When not in use, it is able to rotate freely without significant drag losses.
The new hairpin winding and a direct oil-spray cooling system in the electric motor’s stator contribute substantially to the drive system’s higher efficiency. For example, the fill factor has increased to 60 percent compared to 45 percent for the conventional windings that were used previously.
An electric oil pump in the transmission also contributes to the increased efficiency. Thanks to the rotor oil cooling, Audi was also able to largely dispense with the use of heavy rare earth elements while simultaneously increasing the power density by 20 percent.
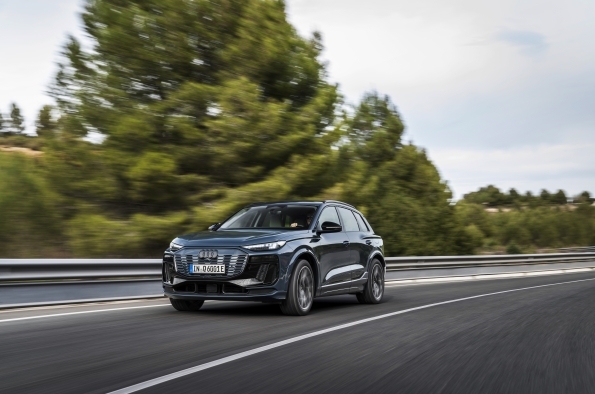
What has Audi changed in the power electronics and the transmission for the PPE?
The power electronics (inverter) controls the electric motor and also converts direct current from the battery into alternating current. The data for the exact control of the inverter is provided by the domain computer HCP1 (high-performance computing platform 1), which is responsible for the drive system and the suspension. Silicon carbide semiconductors are installed in the more powerful version of the water-cooled inverter. Due to their efficiency, which is 60 percent higher, they particularly excel under partial load and are more reliable. As a result, they contribute significantly to the efficiency and higher performance of the PPE electric motors. Due to the 800-volt architecture, thinner wire can also be used for the wiring of the battery and the electric motor. This reduces installation space, weight and consumption of raw materials. Because the system heats up less due to lower heat loss, the cooling system is also smaller and more efficient. The transmission works with dry sump lubrication and an electric oil pump. Nozzles spray the gears directly. This design minimizes friction losses and also reduces installation space.
What technical measures will improve charging performance with the PPE?
The 800-volt architecture, which is required for charging outputs of up to 270 kW, is one of the key factors for high charging performance. The cell chemistry has been optimized to accommodate such a high value. Audi has achieved an optimum balance between energy density and charging performance. The cells developed in collaboration with the supplier offer a high energy density, a significantly reduced cobalt content, and lower resistances for improved charging performance.
In addition to the 800-volt architecture, intelligent thermal management makes a significant contribution to high charging performance and the long service life of the HV battery in the PPE. The most important component is predictive thermal management, which uses data from the navigation system, the route, the departure timer and the customer’s usage behavior to calculate the need for cooling or heating in advance and to provide them both efficiently and at the right time.
If a customer is driving to charge at an HPC charging station included in the route planning, the predictive thermal management system will prepare the DC charging process and cool or heat the battery so that it can charge faster, thus reducing the charging time. If there is a steeper rise ahead, the thermal management system will adjust the HV battery by appropriate cooling to prevent a higher thermal load. If the driver has selected efficiency mode in the drive select menu, the conditioning of the battery
Information Source: Read full article
Oil and gas press covers, Energy Monitor, Climate, Renewable, Wind, Biomass, Sustainability, Oil Price, LPG, Solar, Marine, Aviation, Fuel, Hydrogen, Electric ,EV, Gas,