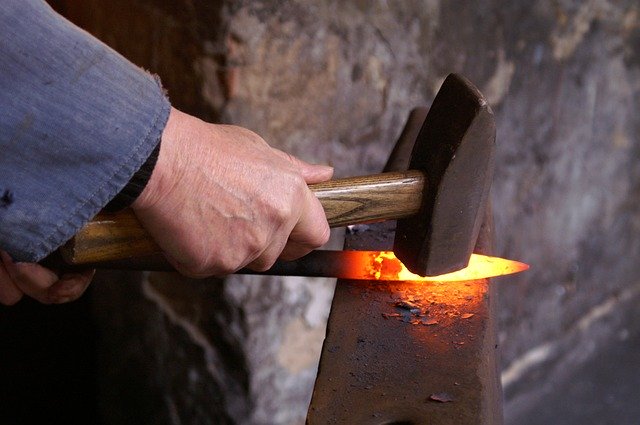
Electra raises $85M to electrify and decarbonize iron and steelmaking with no green premium
Bill Gates-founded Breakthrough Energy Ventures, Amazon, BHP Ventures, Temasek, S2G Ventures, Capricorn Investment Group, Lowercarbon Capital, Valor Equity Partners, Baruch Future Ventures and others back the company
BOULDER, Colo.–(BUSINESS WIRE)–Electra, a green iron company, has raised $85 million to produce Low-Temperature Iron (LTI) from commercial and low-grade ores using zero-carbon intermittent electricity. Electra’s process emits zero carbon dioxide emissions and carries zero green premium, meaning it will cost the same or less than existing production methods powered by fossil fuels.
Electra, founded by entrepreneurs with decades of experience developing complex electrochemical systems, has created a novel process to electrochemically refine iron ore into pure iron at 60 degrees Celsius (140 degrees Fahrenheit) using renewable electricity and then convert the iron to steel using the existing infrastructure of electricity-powered arc furnaces. By comparison, 69% of steel today is made at approximately 1,600 degrees Celsius (2,912 degrees Fahrenheit) using coal, emitting about two tons of carbon dioxide for every ton of steel produced.
Electra’s Oxygen-Decoupled Electrolysis (ODE) process overcomes two interconnected challenges for the steel industry:
- Decarbonizing Steelmaking: The steel industry produces 1.9 billion metric tons of crude steel and causes 3.7 gigatons of direct and indirect carbon dioxide emissions annually, or 10% of the global total. If the steel industry were a country, its carbon emissions would rank third in the world behind China and the United States. Conversion of iron ore into iron accounts for 90% of steelmaking emissions that may be eliminated using Electra’s process.
- The “Iron Ore Challenge”: Commercial iron ores with iron content of 62% or higher are projected to be in short supply by the early 2030s. Hydrogen or natural gas-based steelmaking requires ores with the highest iron content at 67% or above, making the cost and ore supply challenge even more acute for these processes. Electra’s process intakes lower-grade ores with iron content as low as 35% without the additional cost of grinding, beneficiation, and pelletization, enabling zero green premium and a more diverse iron ore supply chain.
“Electra’s iron is the fulcrum to decarbonize steelmaking and to de-risk the iron ore challenge,” said Electra CEO Sandeep Nijhawan. “Our team, starting with a clean sheet, developed an electrochemical process to refine iron ore to high purity iron by radically lowering the process temperature from 1,600 to 60 degrees Celsius, replacing coal energy with intermittent renewable energy, and displacing commercial ores with lower-grade ores that are not being used or are currently treated as waste today. We also have a historic opportunity to decentralize the global iron and steel supply chain and re-shore manufacturing and mining jobs.”
Electra leverages proven electrochemical and hydrometallurgical methods to reach industrial scale with low technical and scaling risks. Electra will complete the build-out of a green-iron refining pilot plant in 2023 at its headquarters in Boulder, CO, and plans to have a commercial-scale demonstration plant qualified by the second half of this decade. The 50-person company recently opened a new office in Boston, MA to help expand its roster of engineers, scientists, and professional support staff.
“Decarbonizing ironmaking is essential for a zero carbon future and an unparalleled trillion-dollar market opportunity,” said Carmichael Roberts of Breakthrough Energy Ventures. “Electrifying cost-effective ironmaking without carbon emissions is a paradigm shift in how steel has been made for centuries by burning fossil fuels. We’re proud to have supported Electra in this critical mission from its founding.”
“Steel is required to make everything from automobiles to buildings, and is one of the hardest sectors to decarbonize,” said Matt Peterson, Director of the Climate Pledge Fund at Amazon. “Amazon is proud to invest in Electra’s green iron technology, which is an important step toward making steel more sustainable, and toward Amazon’s broader goal to reach net zero carbon by 2040.”
“Similar to the shortage of high quality steel scrap, there is a likely shortfall of very low impurity iron ore in forms suitable to feed a transitioning, decarbonizing iron and steel sector,” said Simon C. Wandke an iron ore industry expert and an advisor to Electra. “The potential to use iron ore inputs with high impurity levels including phosphorous, silica, and alumina without any beneficiation, reduces the overall cost of steelmaking, reduces the upstream carbon and ESG footprint and creates new sources of economic value for the iron ore producers.”
Electra plans to forge additional partnerships across the entire steel value chain. Iron ore companies, steel companies, and any company that relies on steel are invited to collaborate with Electra to accelerate the transition to green steel.
“While our mission is inspiring, our work is urgent, fast-paced, and challenging,” concluded Electra CTO Quoc Pham. “To accelerate our mission, we have built a unique culture that fosters collaboration, patience at pace, and a disciplined approach to solving seemingly impossible problems. We continue to expand our magnetic team with a passion for making a gigaton-scale decarbonization impact.”
To learn more and join our mission, visit: www.electra.earth.
ABOUT ELECTRA
Electra, a green iron company, is bending the trajectory of climate change by electrifying iron refining with no green premium. Our products — pure green iron and other green feedstocks — remove gigatons of carbon dioxide emissions from steel production and other hard-to-abate industries, accelerating a return to a healthy carbon balance on earth. The company is headquartered in Boulder, CO with a development facility in Boston, MA.
Contacts
Molly Hendriksen
BerlinRosen
electra@berlinrosen.com
(510) 418-2511
Simon Lomax
Electra Corporate Affairs Advisor