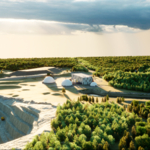
NMG Issues Results of Feasibility Study for its Integrated Ore-to-Anode-Material Model
This news release constitutes a “designated news release” for the purposes of the Company’s prospectus supplement dated January 21, 2022, to its short form base shelf prospectus dated May 19, 2021, as amended by amendment no. 1 dated January 19, 2022.
- NMG is developing a turnkey natural graphite operation with competitive advantages due to its privileged location, vertical integration, cost structure, ESG credentials and experienced team.
- The Company’s Phase-2 Matawinie Mine and Bécancour Battery Material Plant projects, located within a 150-km radius of Montréal, Québec, show attractive economics and robust operational parameters underpinned by a large mineral property, NMG’s proprietary technologies, and clean hydroelectricity powering its operations.
- The Feasibility Study of NMG’s integrated operation indicates a 21% after-tax IRR and NPV of C$ 1,581 million based on current projections of pricing prepared by a third-party expert for high-purity flakes and advanced graphite materials.
- NMG’s integrated production flowsheet provides the flexibility to distribute graphite concentrate per flake size and market demand in order to cater to the most profitable segments.
- NMG’s phased approach has helped de-risk NMG’s projects while accelerating the engineering of Phase-2 operations, generating process and cost optimization, and supporting commercialization with potential customers.
- NMG is designing a mine of the future, targeted to be all-electric, complemented by clean advanced beneficiation facilities in order to provide battery and EV manufacturers with responsibly extracted, environmentally transformed, and locally sourced green anode material.
- Shareholders and analysts are invited to attend an Investor Briefing at 10:30 a.m. ET hosted by NMG’s Management Team via webcast: https://us06web.zoom.us/webinar/register/WN_XA0uyzAQTBiPinZmx3pvuA
MONTRÉAL–(BUSINESS WIRE)–$NMG #ESG–Developing a local, carbon-neutral and traceable turnkey supply of advanced materials for the Western World, Nouveau Monde Graphite Inc. (“NMG”, “Nouveau Monde” or the “Company”) (NYSE: NMG, TSXV: NOU) releases the results of its feasibility study (the “Study”) completed in accordance with the National Instrument 43-101 (“NI 43-101”) for its integrated business operation comprised of the Phase-2 Matawinie Mine and Bécancour Battery Material Plant projects. The Study, conducted by engineering firm BBA Inc. (“BBA”) with the support of various technical consultants, has demonstrated strong economics for NMG’s model as the battery and electric vehicle (“EV”) manufacturers seek alternatives for sourcing their graphite-based solutions amidst growing demand and projected structural deficit of production in the next decade. The Company is ideally positioned to cater to the North American and European markets with its large graphite deposit, proprietary ecotechnologies, demonstrated production capacity thanks to its Phase-1 operations, as well as preferential jurisdiction advantages including clean hydropower, flexible logistical base and stable fiscal and political environment.
Updating resources and reserves, operational, and financial metrics of the Matawinie Mine 2018 bankable feasibility study (effective as of July 10, 2018 and issued on December 10, 2018), the Study also layered the production and economics structure of the Bécancour Battery Material Plant, the process and engineering optimizations generated in recent months, the latest market pricing as per Benchmark Mineral Intelligence’s assessment, as well as capital expenditures (“CAPEX”) and operating expenses (“OPEX”) profile amidst current economic conditions. These combined parameters for a projected annual average production of 103,328 tonnes per annum (“tpa”) of high-purity flake graphite concentrate at the Matawinie Mine and 42,616 tpa of anode material plus 3,007 tpa of purified jumbo flakes at the Bécancour Battery Material Plant, using a portion of Matawinie’s production as feedstock, indicate an after-tax net present value (“NPV”) of C$ 1,581 million and internal rate of return (“IRR”) of 21%.
Arne H Frandsen, Chair of NMG, said: “Market trends have accelerated in past months and while inflation and logistics turbulences present a more challenging environment, we have demonstrated our graphite expertise, advanced manufacturing capacity and complex project management skills to execute our vision of an integrated green anode material production. The successful upstream integration is designed to ensure that we have access to high-quality, responsible feedstock for decades to come, and provides battery and EV manufacturers with the assurance of a traceable, local, and carbon-neutral supply.”
Table 1: Economic highlights of NMG’s integrated Phase-2 graphite operations.
ECONOMIC HIGHLIGHTS |
Matawinie Mine |
Bécancour Battery Material Plant |
INTEGRATED NMG MODEL |
Pre-tax NPV (8% discount rate) |
C$ 986 M |
C$ 1,374 M |
C$ 2,360 M |
After-tax NPV (8 % discount rate) |
C$ 571 M |
C$ 1,010 M |
C$ 1,581 M |
Pre-tax IRR |
28.2% |
22.8% |
24.6% |
After-tax IRR |
22.2% |
20.4% |
21.0% |
Pre-tax payback |
3.2 years |
4.3 years |
3.9 years |
After-tax payback |
3.7 years |
4.5 years |
4.2 years |
Annual average production |
103,328 tonnes of graphite concentrate |
42,616 tonnes of anode material 3,007 tonnes of purified jumbo flakes 18,384 tonnes of by-product fines |
– |
Life of mine (“LOM”) |
25 years |
– |
– |
Initial CAPEX |
C$ 481 M |
C$ 923 M |
C$ 1,404 M |
Annual OPEX |
C$ 58 M |
C$ 136 M |
C$ 195 M |
CAPEX and OPEX were established from test work results, Phase-1 operations, supplier quotations and consultant’s in-house databases. Estimates being currently at the market’s peak as influenced by inflationary trends, NMG and its consulting firms have refined design, engineering, and construction parameters to enable cost optimization and competitive pricing of NMG’s production. Québec’s affordable clean hydropower underpins the Company’s technologies, economics structure and carbon-neutrality commitment.
NMG’s integrated business model, with a secured feedstock, close-by operations at the western market’s doorstep and operational flexibility to adapt production based on demand, represents a stable and cost-effective structure in today’s everchanging macroeconomics.
Eric Desaulniers, Founder, President, and CEO of NMG, commented: “We have come a long way from our initial Matawinie Mine project to develop an integrated operation tailored to the market’s technical requirements and sourcing strategy. NMG is positioning itself as North America’s largest, fully integrated natural graphite production to relieve battery and EV manufacturers from their overreliance on Chinese production. With attractive economics, strong ESG credentials, demonstrated execution capacity, and high-purity advanced materials, we are set to provide a turnkey large-scale solution for the booming local battery value chain. Our significant forecasted incremental annual operating profit potential is a testimony that it is possible to embrace sustainable development and profitability to the benefit of all stakeholders.”
Product Offering and Market
The integrated material flowsheet developed by NMG is designed to leverage the distribution of graphite concentrate flake sizes to be produced at the Phase-2 Matawinie Mine by catering to the most profitable market segments. Jumbo to coarse flakes will be destined to high-purity, high-margin specialty and traditional markets at a LOM average price of C$ 2,135 per tonne. While fine to intermediate flakes will be transformed into coated spherical purified graphite (“CSPG”) at the Phase-2 Bécancour Battery Material Plant for sales as anode material for lithium-ion battery applications at a LOM average price of C$ 11,540 per tonne. A portion of jumbo flakes will also undergo refinement at the Bécancour Battery Material Plant to produce purified jumbo flakes for niche applications such as heat dissipators in 5G technologies and bipolar plates in hydrogen fuel cells. By-products from this facility will also be sold to optimize the Bécancour basket price.
Selling prices were calculated using forecasts provided by Benchmark Mineral Intelligence, an IOSCO-regulated price reporting agency and market intelligence publisher for the lithium-ion battery to EV supply chain. They were estimated for the North American market where the Company is expected to have competitive advantages over international producers, namely its carbon-neutral footprint, multimodal logistical base, stable political jurisdiction and exclusion from U.S. import tariffs on graphite.
Pressure caused by gigafactories development across the world, limited production capacity impacted by Chinese pandemic measures and turbulent logistics is reflected in the year-over-year flake graphite price increase of 37% (Benchmark Mineral Intelligence, May 2022). The global lithium-ion battery production capacity pipeline to 2031 now reaches 6,660 GWh, driving associated projections for graphite demand to 7,993,000 tpa, the largest of all battery metals.
Mineral Resource and Reserves
The mining property (the “Mining Property” or the “Tony Block”) presently consists of 159 contiguous map-designated claims totalling 8,266.42 hectares (“ha”) wholly owned (100%) by NMG. The Matawinie Mine project lies within the municipality of Saint-Michel-des-Saints, Québec, Canada, approximately 120 km as the crow flies north of Montréal.
Exploration work on the Mining Property targeted graphite mineralization and consists to date of airborne geophysics, prospecting, ground TDEM surveying, trenching/channel sampling and core drilling. Surface and core samples were also collected for metallurgical and geomechanical tests. Exploration work uncovered significant crystalline flake graphite mineralization ultimately leading to the identification of Mineral Resources and Reserves.
Mineral Resources have been estimated for the West Zone of the Mining Property. These Mineral Resources are based on 8,274 assay intervals collected from 27,888.24 m of core drilling and three (3) surface trenches providing 207 channel samples. Proper quality control measures, including the insertion of duplicate, blank and standard samples, were used throughout the exploration programs and returned within acceptable limits.
Table 2: Current Pit-Constrained Mineral Resource Estimate for the West Zone1
Mineral Resource Category2 |
Current Resource (May 20, 2022) 7 |
||
Tonnage (Mt)5,6 |
Grade (% Cg)3 |
Contained Graphite (Mt) |
|
Measured |
28.5 |
4.28 |
1.22 |
Indicated |
101.8 |
4.26 |
4.33 |
Measured + Indicated |
130.3 |
4.26 |
5.55 |
Inferred4 |
23.0 |
4.28 |
0.98 |
|
A combined Mineral Resource of the South-East and South-West zones is also present on the Mining Property. While these deposits are part of the Property, they have not been studied to be integrated in the Mineral Reserves or the mine plan.
The table below presents the Mineral Reserves which have been estimated for the West Zone of the Matawinie Deposit.
Table 3: Matawinie Mineral Reserves for the West Zone
Category |
Tonnage (Mt) |
Grade (% Cg) |
Contained Graphite (Mt) |
Proven |
17.3 |
4.16 |
0.7 |
Probable |
44.3 |
4.26 |
1.9 |
Proven & Probable |
61.7 |
4.23 |
2.6 |
The Qualified Person for the Mineral Reserve Estimate is Jeffrey Cassoff, P.Eng., of BBA Inc. The effective date of the estimate is July 6, 2022. Mineral Reserves were estimated using a graphite concentrate average selling price of C$2,135/tonne, and consider a 2% royalty, and selling costs of C$47.92/tonne. An average grade of 97% was considered for the graphite concentrate. A metallurgical recovery of 93% was used. A cut-off grade of 2.20% Cg was used. The strip ratio for the open pit is 1.16 to 1. The Mineral Reserves are inclusive of mining dilution and ore loss. The reference point for the Mineral Reserves is the primary crusher. Totals may not add due to rounding. |
Matawinie Mine
The Matawinie Mine will leverage the West Zone deposit with an average production of 103,328 tpa of high-purity graphite concentrate over the LOM. The project demonstrates exceptional potential due to its significant high-purity Mineral Reserves and low-cost operational model, coupled with a skilled workforce, high-quality infrastructure, including paved roads and hydroelectricity, as well as the dynamic regional business ecosystem.
The deposit will be mined using conventional open-pit mining methods consisting of drilling, blasting, loading, and hauling. Estimation of the Mineral Reserves included pit optimization, pit design, mine scheduling, and the application of modifying factors to the Measured and Indicated Mineral Resources. To maximize the NPV, mining phases have been designed and incorporated into the mining sequence to defer waste rock stripping and provide a balanced blended feed grade for the concentrator over the LOM. The mine plan is successful at achieving the targeted concentrate production with a strip ratio of 1.16:1 and an average grade of 4.23% Cg over the 25‑year LOM.
A concentrator will be built adjacent to the pit. The concentrator was designed based on the results from the metallurgical testing at NMG’s Phase-1 mineral processing facility plant and at external labs. Through crushing, milling, flotation, cleaning, and drying, the ore is concentrated to attain 97% Cg and classified per flake size. Water recycling is maximized throughout the process.
Table 4: Graphite Concentrate Size Fraction Proportion
Graphite Concentrate Flakes Size Fraction |
Proportion |
|
Jumbo (+50 mesh) |
14.8% |
|
Coarse (-50+80 mesh) |
33.4% |
|
Intermediate (-80+150 mesh) |
27.7% |
|
Fine (-150 mesh) |
24.1% |
Tailings produced by the concentrator will be separated into non-acid generating (“NAG”) and potentially‑acid generating (“PAG”) for co-disposal with waste rock. A co‑deposition storage facility will be located at surface and as of Year 8, tailings will be returned to the pit using the co-disposal system. The deposit will be mined from south to north to ensure adequate space is available for in‑pit backfilling. See Environmental Design & Carbon Neutrality Commitment section for additional information.
As part of its electrification strategy, NMG is committed to having both heavy equipment used for mining operations and ore concentration and processing activities become fully electric within the first five years of production. NMG’s electrification plan is not presented in this Study as active planning and development are ongoing with Caterpillar Inc., which is expected to supply the equipment using their Job Site Solution service model. With this model, NMG would pay for machine use on an hourly basis which includes machine supply and maintenance (parts and service) and a fleet management system. Electrical trucks and equipment would be introduced into the mining fleet as they become available. Projected to be the world’s first all-electric open-pit mine, the Matawinie Mine could reduce CO2 emissions by over 300,000 tonnes over the mine’s lifespan.
Table 5: Operational and Economic Highlights of the Matawinie Mine
Parameters |
|
LOM |
25 years |
Nominal annual processing rate |
2.55 M tonnes |
Stripping ratio (LOM) |
1.16:1 |
Average grade (LOM) |
4.23% Cg |
Average recovery |
93% |
Average annual graphite concentrate production (LOM) |
103,328 tonnes |
Finished product purity |
97% Cg |
CAPEX |
C$ 481 M |
Annual OPEX |
C$ 58 M |
OPEX cost per tonne of graphite concentrate |
C$ 565/tonne |
Matawinie average basket price (LOM) |
C$ 2,135/tonne |
All governmental permits and municipal authorizations pertaining to exploration, geotechnical, hydrogeological, and early preparatory works to date have been obtained. The ministerial decree authorizing the Matawinie Mine (Decree # 47-2021) was granted by the Québec Government on January 20, 2021; the latest operational parameters will be presented to governmental authorities for adjustment.
Early works for the Matawinie Mine started in Q2-2021 with activities related to tree clearing, construction of the nearly 8-km access road, preparation of the industrial pad, and civil works for environmental infrastructure.
In striving to limit potential impacts and plan beyond the LOM, the Company has developed the Matawinie Mine with environmental and social considerations at the forefront. NMG has and continues to actively engage with the local community and the Atikamekw First Nation. NMG has signed a collaboration and benefit-sharing agreement with the Municipality of Saint-Michel-des-Saints (2020) as well as a framework agreement (2018) and a pre-development agreement (2019) with the Atikamekw First Nation. The Company is actively progressing towards the elaboration of the impact and benefit agreement with the Atikamekw First Nation for the Phase-2 Matawinie Mine to maximize opportunities for Indigenous workers, contractors, and the community.
Bécancour Battery Material Plant
NMG’s advanced manufacturing operations will be regrouped at its Phase-2 Bécancour Battery Material Plant located in Bécancour, Québec, approximately 150 km northeast of Montréal, on the Saint Lawrence River. The robust local infrastructure provides the Company with a direct supply of required chemicals in addition to affordable hydroelectricity, a skilled workforce, and a multi-modal logistical base that includes a major international port in proximity to U.S. and European markets. Bécancour is rapidly attracting important industrial players in the battery materials and cell manufacturing space, supported by the Québec Government’s battery hub strategy. Twenty industrial and commercial projects are planned or under study, including BASF, GM-Posco, Vale and Nemaska Lithium.
In 2021, NMG purchased a 200,000-m² land in the Bécancour industrial park, adjacent to its chlorine supplier’s facility – Olin Corporation, to build its integrated manufacturing facility of anode material for lithium-ion batteries. The property presents no environmental limitations for construction. It offers all necessary infrastructure to have a safe and direct pipeline of chemical supply from Olin as well as quick access to rail, port, and road for both importing raw materials and exporting final products throughout North America and Europe.
Regrouping onsite all beneficiation units, the Bécancour Battery Material Plant is designed to receive approximately 63,775 tpa of graphite concentrate from the Matawinie Mine to be transformed into 42,616 tpa of CSPG, 3,007 tpa of purified flakes and 18,384 tpa of by-product fines, a valuable graphite material.
For CSPG production, the finest flake size fraction graphite concentrate will undergo micronization and spheronization (“shaping”), purification and coating. A portion of the jumbo flake production from the Matawinie Mine will be treated onsite through purification only to produce purified jumbo flakes.
The shaping process, essentially a mechanical transformation, reduces the flake size (micronization) to D50 of approximately 10 to 20 microns and rounds graphite material (spheronization) to increase the density of the spherical graphite for battery use. Shaping will also generate by-product fines to be sold as carbon riser.
NMG’s proprietary carbochlorination purification process elevates graphite materials to ≥99.95% Cg while respecting purity specifications of end-users. The carbochlorination process involves the injection of chlorine gas into furnaces at high temperatures to remove impurities contained in the graphite. Leveraging Québec’s abundant, clean, and affordable hydropower, the Company’s technology avoids using hydrofluoric acid in favor of high temperatures and the addition of chlor-based reagent, hence providing a greener and more sustainable alternative to that currently used in traditional anode material production. Production at NMG’s Phase-1 purification facility has demonstrated the performance of this ecotechnology with large-scale samples produced at 99.99% purity. Piloting is ongoing and set to continue over H2-2022 to finalize the scope of the purification sector of the plant.
The ultimate beneficiation step, coating is instrumental to battery technology. By applying a nanometric layer of amorphous carbon on the surface of spheronized purified graphite, coating helps create a stable electrolyte interface layer in the battery system and increase initial coulombic efficiency and discharge capacity, thus extending the battery performance over time. NMG’s coating technology is projected to reduce the energy consumption of this process up to 25% compared to the dominant manufacturing operations, with a minimal environmental footprint thanks to the Company’s access to clean hydropower and its strong ESG operational parameters. The module built at NMG’s Phase-1 plant will be replicated and scaled up for the Phase-2 Bécancour Battery Material Plant. The technology provides versatility for the use of different precursors as research and development (“R&D”) advances.
Piloting of all Phase-1 battery material modules is ongoing to produce large samples for battery manufacturers in order to accelerate the commercial qualification of the battery-grade commercial products.
Table 6: Operational and Economic Highlights of the Bécancour Battery Material Plant
Parameters |
|
Annual throughput |
63,775 tonnes |
CSPG yield |
≥70% |
Annual CSPG production |
42,616 tonnes |
Annual purified jumbo flake production |
3,007 tonnes |
Annual by-product fines production |
18,384 tonnes |
Finished product purity |
≥99.95% |
CAPEX |
C$ 923 M |
Annual OPEX |
C$ 136 M |
OPEX cost per tonne of CSPG throughput1 |
C$ 2,249/tonne |
Bécancour average basket price |
C$ 8,172/tonne |
|
The Bécancour Battery Material Plant will be organized by process sectors, with dedicated facilities for shaping, purification, and coating, plus support services. This modular facility is designed with a capacity to expand as demand increases in battery and specialty markets.
Contacts
MEDIA
Julie Paquet
VP Communications & ESG Strategy
+1-450-757-8905 #140
INVESTORS
Marc Jasmin
Director, Investor Relations
+1-450-757-8905 #993