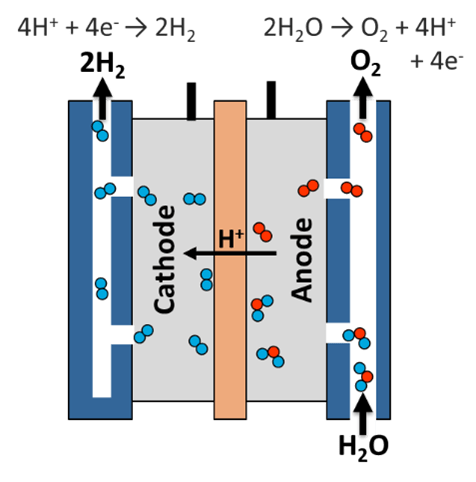
OCOchem Advances Hydrogen Formate Electrolyzer Process By 10x To Create World’s Largest Industrial Scale CO2 Electrolyzer Cell
Collaboration with US Army develops safer and sustainable organic platform molecule at lower cost than existing fossil-based pathways.
RICHLAND, Wash.–(BUSINESS WIRE)–OCOchem today announced completion of its Phase II project with United States Army to develop and test its 15,000cm2 formate electrolyzer cell. The company scaled up from 10 to 15,000 cm2 over four steps in three years to achieve an industrial scale form factor. As a result of this new benchmark, OCOchem’s CO2 electrolyzer is 650% larger than other platforms, its final industrial scale cell size and is now scaling out into multi-cell stacks in a larger scale pilot plant.
OCOchem specializes in making an organic platform molecule known as hydrogen formate through CO2 electrolysis, leveraging clean electricity and advanced engineering technologies, instead of sunlight and plant biology, to transform carbon dioxide and water into valuable carbon-based molecules. Formate serves as a crucial precursor chemical, providing both carbon and hydrogen together in a single liquid molecule instrumental in synthesizing a diverse array of derivative materials, chemicals, and fuels. It is the liquid form of energized CO2 ready for use. OCOchem’s process to make formate is known as “electro-formation” and is designed for high (104%) carbon-to-product efficiency, high (85%) energy efficiency, room temperature and pressure operation, and lack of waste by-products.
The CO2 electrolyzer produces a safer and sustainable liquid platform chemical, hydrogen formate, which can be made at a lower cost than existing fossil-based pathways as it uses CO2, water, and clean electricity as its only raw materials. Formate is also used as a platform molecule to make many other molecules, which constitute more than 20% of the $3.5 trillion/year global chemical market.
“CO2 electrolysis has historically been an academic cottage industry with little work done on cells much larger than a baseball card. The OCOchem approach has been different, focusing on rapid step change scale-up and then iterating much of the design with every 10x scale-up increment. What works at a tiny scale is not what works at a larger scale. We knew that and our constraints going in. The innovative modification and integration of off-the-shelf industrial-grade components, parts and systems, custom chemistry, and in-house fabrication of large-scale gas diffusion electrodes we deploy allows us to ‘live within constraints.’ Constraints are awesome because they force you to challenge and change the non-obvious things. It is about constant questioning,” said OCOchem CEO and Co-Founder Todd Brix.
Adds Brix: “Doing CO2 electrolysis, at high efficiencies, throughput, and product concentration at an industrial scale size cell, 650% larger than previously reported 2000cm2 size, is a major step forward to industrial commercialization. The challenges of an industrial-scale cell relative to even 10x smaller scale cells are completely different in type, not just in size, and require very different process chemistries, reactor designs and electrode fabrication techniques our team has iteratively developed to reach new industry benchmarks.”
Central to a sustainable future is the concept of regenerated carbon, or carbon harvesting, which emphasizes the endless circular reutilization of CO2. This aligns with the broader principle of waste recycling and reprocessing, enabling a circular economy where products and their by-products, after use, are then decomposed into molecules and reused, reflecting the natural processes of our planet where solar energy and plants continuously cycle CO2 and water, maintaining ecological balance.
“CO2 regeneration is a much more impactful way to reduce CO2 emissions using captured CO2. Instead of just moving and burying a ton of CO2 and hoping it doesn’t come back out of the ground, you instead convert that CO2 into a value-added useful product which displaces the same product made conventionally from fossil fuels and avoids the 5-10 tons of CO2 emissions associated with fossil fuel use as a feedstock as well as use of fossil fuel process energy used to make it,” explains Todd Brix.
“Carbon is the backbone of life, and CO2 has historically been the source of carbon that life uses, not fossil fuels. The CO2 electrolysis technology being developed by OCOchem will enable humankind to re-obtain this state of carbon sourcing and balancing,” said Dr. Robert Weber, former Senior Research Scientist who led early work at Pacific Northwest National Laboratory into formate as a liquid hydrogen carrier.
Formate is utilized in everyday applications such as silage preservatives, corrosion-free deicing salts, drilling fluids, fertilizers, and in the manufacture of leather and clothing. It also plays a crucial role in tire and rubber production, bacterial disinfection, and waste and feed water treatment, and as an emerging liquid carrier of hydrogen and carbon oxides.
“OCOchem is on its way to becoming a central player in the development of a circular carbon economy. Our chief objective is to use clean electricity to regenerate past and present carbon dioxide emissions into value-added products. Instead of harvesting carbon from fossil fuels or crops we can just directly harvest carbon from the CO2 in the air and point sources and make most of the organic molecules we need from that. This approach not only avoids extracting and releasing more carbon from fossil fuels but also reduces pressure on biodiversity and food and feed supplies by reducing the need to convert forests and grasslands into molecule crops,” said Brix.
About OCOchem
Located in Richland, Washington, OCOchem’s founding mission is to “use, not waste, CO2.” This mission is realized by converting recycled CO2 into a “green” platform organic molecule, using just clean electricity and water, and doing that at a progressively lower cost than the fossil-fueled pathway for making the same molecule. By making a “platform” organic molecule, it can be used as a building block to synthesize a wide range of other molecules that make up most of the materials, chemicals, and fuels our society uses that are today made primarily from fossil fuels. This approach inverts the current economic incentives to extract, combust, and release the carbon embodied in fossil fuels by providing lower-cost substitutes made from CO2. For more information visit: www.ocochem.com
Contacts
Steven Gottlieb