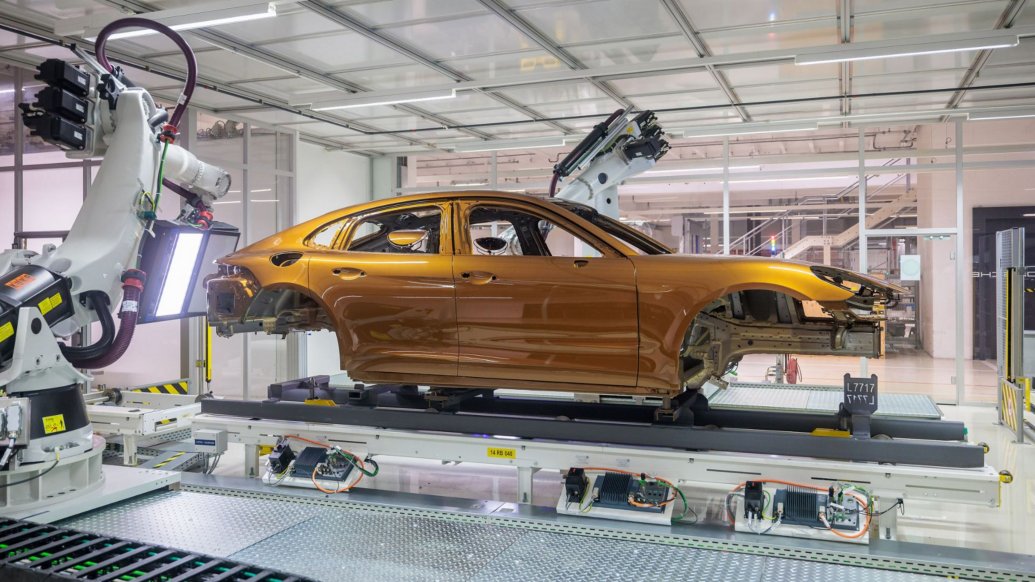
Porsche paint shop
London, January 22, 2025 (Oilandgaspress) –-Robots, artificial intelligence – and a human touch. How the Porsche plant in Leipzig ensures only the finest finishes leave the paint shop. Until relatively recently, these labour-intensive and time-consuming inspections would have to be carried out manually – and, even with the keenest of eyes, always with the natural risk of human error. With modern technology, however, this process in the paint shop at the Porsche plant in Leipzig has been significantly streamlined. Team members in the inspection area are assisted by an automatic defect detection system. Equipped with powerful sensors, these robot arms scan the entire outer surface of the body shell of every series-production car produced at Leipzig.An image is captured every 2.5 millimetres, resulting in about 100,000 pictures being gathered during the 72-second inspection cycle. These extensive scans are analysed by a network of 10 powerful image-processing computers searching for even the smallest of imperfections. Pinholes, craters and particles of dust or other debris (known as ‘inclusions’) are identified with precision and total objectivity, which presents a major advantage over the subjective nature of manual visual inspections.
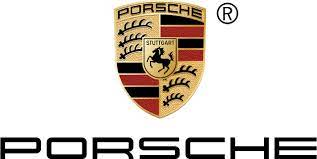
If a defect is found, its exact location is recorded with millimetre accuracy. The complete data is then forwarded to the finishing line, where the skilled team carries out the necessary paint corrections. The location of the defect is presented to the team members via a digital model, which is enhanced with high-resolution close-up images and details of the category of defect. This enables the team to quickly target the issue and choose the appropriate method of rectification. Read More