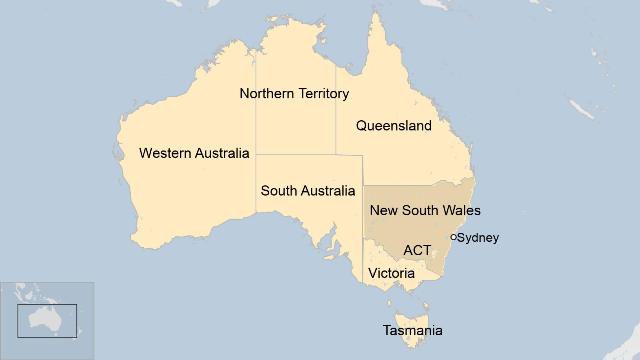
Sypris Wins Award for the Gorgon Project in Western Australia
Specialty Closures for Use in Carbon Capture and Storage Systems
LOUISVILLE, Ky.–(BUSINESS WIRE)–$SYPR–Sypris Technologies, Inc., a subsidiary of Sypris Solutions, Inc. (Nasdaq/GM: SYPR), announced today that it has recently received an award to supply specialty high-pressure closures for use in the Gorgon Project to support the optimization of the existing carbon capture and storage facilities. Shipments under this award are anticipated to be completed by year-end 2024. Terms of the order were not disclosed.
The Gorgon Project is one of the world’s largest natural gas projects. The project is located on Barrow Island, Australia and is comprised of three trains with a combined capacity of 15.6 million tonnes of gas per annum, and a domestic gas plant, according to news sources. This project is expected to be an important pillar of the Australian economy for decades to come. Unlocking this energy is expected to put Australia in a prime position to meet future demand and provide a clean-burning fuel, both at home and overseas.
The project includes CO2 injection and is poised to reach a significant milestone at its Gorgon LNG facility, injecting and trapping five million tonnes of greenhouse gas (carbon dioxide equivalent, CO2e) into a giant sandstone formation two kilometers under Barrow Island, since safely starting the system in August 2019, according to news sources. The milestone would represent the largest volume of injection achieved within this timeframe by any environmental carbon capture and storage system of comparable specifications. Injecting five million tonnes of CO2 is equivalent to taking more than 1.6 million passenger vehicles off Australia’s roads for a year.
Sypris has agreed to manufacture and supply its Tube Turns®-branded specialty, high-pressure Tool-less® closures for use on the filtration systems for the project. These closures will be 44 inches in diameter, will be rated to a pressure of 710 psi and include full wetted surface overlay with Inconel Alloy 625, a nickel-based superalloy that possesses high strength properties and resistance to elevated temperatures.
Brett Keener, General Manager, commented, “Sypris continues to be a leader in supplying high-pressure specialty closures to support energy projects globally. By leveraging our extensive engineering design and manufacturing expertise, we believe we are uniquely qualified to support these types of demanding requirements. We are proud to be a part of a project with a goal to help provide clean, reliable energy and reduce the world’s carbon footprint.”
Sypris Technologies, Inc., Tube Turns Products, is a global leader in the manufacture of custom engineered products for high pressure critical applications serving multiple industries such as the oil and gas pipeline, hydrocarbon and petrochemical processing, food, pharmaceutical, water and utility since 1927. Headquartered in Louisville, Kentucky, the Company’s products are marketed worldwide, and can be found in projects ranging from the Trans-Alaska Pipeline and Strategic Petroleum Reserve in the U.S. to the Tengiz Oil Field in Kazakhstan and the Bonny Island Gas Field in Nigeria. For more information about the Company, visit its Web site at www.sypris.com.
Forward-Looking Statements
This press release contains “forward-looking” statements within the meaning of the federal securities laws. Forward-looking statements include our plans and expectations of future financial and operational performance. Each forward-looking statement herein is subject to risks and uncertainties, as detailed in our most recent Form 10-K and Form 10-Q and other SEC filings. Briefly, we currently believe that such risks also include the following: our failure to achieve profitability on a timely basis by steadily increasing our revenues from profitable contracts with a diversified group of customers, which would cause us to continue to use existing cash resources or require us to sell assets to fund operating losses; the fees, costs and supply of, or access to, debt, equity capital, or other sources of liquidity; risks of foreign operations, including foreign currency exchange rate risk exposure, which could impact our operating results; cost, quality and availability or lead times of raw materials such as steel, component parts , natural gas or utilities including increased cost relating to inflation; dependence on, retention or recruitment of key employees and highly skilled personnel and distribution of our human capital; the cost and availability of full-time accounting personnel with technical accounting knowledge to execute, review and approve all aspects of the financial statement close and reporting process; the cost, quality, timeliness, efficiency and yield of our operations and capital investments, including the impact of inflation, tariffs, product recalls or related liabilities, employee training, working capital, production schedules, cycle times, scrap rates, injuries, wages, overtime costs, freight or expediting costs; volatility of our customers’ forecasts and our contractual obligations to meet current scheduling demands and production levels, which may negatively impact our operational capacity and our effectiveness to integrate new customers or suppliers, and in turn cause increases in our inventory and working capital levels; our failure to successfully complete final contract negotiations with regard to our announced contract “orders”, “wins” or “awards”; significant delays or reductions due to a prolonged continuing resolution or U.S. government shut down reducing the spending on products and services; adverse impacts of new technologies or other competitive pressures which increase our costs or erode our margins; breakdowns, relocations or major repairs of machinery and equipment, especially in our Toluca Plant; the termination or non-renewal of existing contracts by customers; the costs and supply of insurance on acceptable terms and with adequate coverage; the costs of compliance with regulatory or contractual obligations; pension valuation, health care or other benefit costs; our reliance on revenues from customers in the oil and gas and automotive markets, with increasing consumer pressure for reductions in environmental impacts attributed to greenhouse gas emissions and increased vehicle fuel economy; our failure to successfully win new business or develop new or improved products or new markets for our products; war, geopolitical conflict, terrorism, political uncertainty, or disruptions resulting from the Russia-Ukraine war or the Israel and Gaza conflict, including arising out of international sanctions, foreign currency fluctuations and other economic impacts; our reliance on a few key customers, third party vendors and sub-suppliers; inventory valuation risks including excessive or obsolescent valuations or price erosions of raw materials or component parts on hand or other potential impairments, non-recoverability or write-offs of assets or deferred costs; disputes or litigation involving governmental, supplier, customer, employee, creditor, stockholder, product liability, warranty or environmental claims; failure to adequately insure or to identify product liability, environmental or other insurable risks; unanticipated or uninsured product liability claims, disasters, public health crises, losses or business risks; labor relations; strikes; union negotiations; costs associated with environmental claims relating to properties previously owned; our inability to patent or otherwise protect our inventions or other intellectual property rights from potential competitors or fully exploit such rights which could materially affect our ability to compete in our chosen markets; changes in licenses, or other legal rights to operate, manage our work force or import and export as needed; cyber security threats and disruptions, including ransomware attacks on our systems and the systems of third-party vendors and other parties with which we conduct business, all of which may become more pronounced in the event of geopolitical conflicts and other uncertainties, such as the conflict in Ukraine; our ability to maintain compliance with the Nasdaq listing standards minimum closing bid price; risks related to owning our common stock, including increased volatility; possible public policy response to a public health emergency, including U. S or foreign government legislation or restrictions that may impact our operations or supply chain; or unknown risks and uncertainties and the risk factors disclosed in Item 1A of our Annual Report on Form 10-K for the fiscal year ended December 31, 2022. We undertake no obligation to update our forward-looking statements, except as may be required by law.
Contacts
Brett H. Keener
General Manager
(502) 774-6271